CNC slotting machines
The increasingly popular CNC machine tools facilitate slotting processes, expanding technological possibilities, especially in the scope of unit production, at low implementation costs. Although in practice techniques considered niche are still used, the spread of numerically controlled machines has resulted in adaptations of certain manufacturing techniques to the extent possible in terms of their use on CNC machine tools, writes Dr. Eng. Radosław Morek in MM Magazyn Przemysłowy.
The increasingly popular CNC machine tools facilitate slotting processes, expanding technological possibilities, especially in the scope of unit production, at low implementation costs. Although in practice techniques considered niche are still used, the spread of numerically controlled machines has resulted in adaptations of certain manufacturing techniques to the extent possible in terms of their use on CNC machine tools, writes Dr. Eng. Radosław Morek in MM Magazyn Przemysłowy.
The slotting process takes place primarily on technological machines called slotting machines. This type of manufacturing technique is also used in the machining of gears (slotting using the Maag method or Fellows method). The discussed processing also uses slotting attachments, which can be used on milling machines. A method used in parallel is planing - slotting is distinguished by the fact that it is carried out primarily in the vertical direction and on shorter sections. In each machining cycle, it enters the material of the workpiece and exits it. Each time, it also penetrates the material not gradually, but with the full cross-section of the cutting layer, which significantly – negatively – affects the durability of the tool blade. Another disadvantage of this type of processing is the occurrence of a return (idle) movement, which reduces the efficiency of processing.
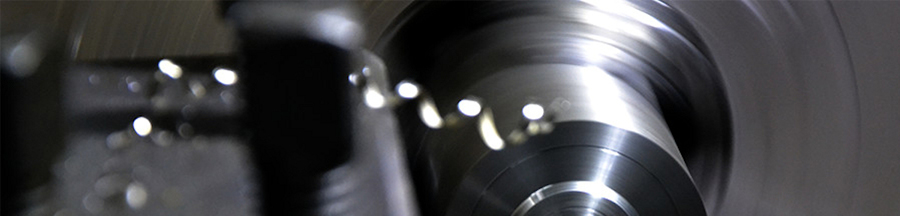
Processing surfaces and parameters
Slotting is used to process surfaces with rectilinear generators, primarily to make rectilinear external and internal keyways, as well as to undercut, chamfer and create profile shapes. This results from the fact that the main movement in this process is a reciprocating movement performed cyclically, which ensures the continuity of processing.
Depending on the shape being processed, it may be necessary to make tools with a specific geometry and blade outline. The techniques used today even allow slotting of helical grooves, but this depends on the capabilities of the control system of a given machine tool. Moreover, such performance is in opposition to the classic definition of slotting, which emphasizes the processing of surfaces with rectilinear generators.
The machining parameters include the thickness and width of the cutting layer, feed speed, cutting speed (working) and idle (return) movement speed. The thickness of the cutting layer is usually from 0.05 to 0.15 mm, depending on the type of material being processed. In turn, the length of the chiselled outline is usually in the range of 2 to even 20 mm. In the case of larger holes to be processed, it is recommended to perform chiselling in two stages: roughing and finishing. The first stage in terms of quality (geometric accuracy, surface roughness) is aimed at machining with the highest possible efficiency.
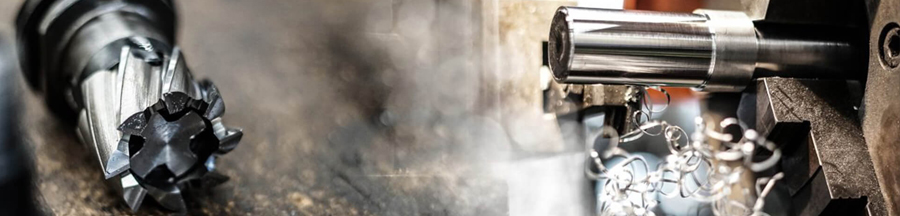
Cutting tools
The cutting tool in the chiselling process is a single-edge knife. Since its width must correspond to the desired width of the groove being made, it can be considered a shape tool. Chamfering the corners of the inserts (0.1–0.2 × 45 degrees) increases their service life compared to inserts with a sharp edge. The keyway is made in several passes of the tool.
A single-edge knife has a relatively low price, making chiseling economically advantageous in single-piece and small-batch production. The set includes a holder, cutting insert and a selected adapter (square or prismatic) that also allows for classic use in a chiseling machine. The adapter allows for angular positioning of the tool – in four positions at an angle of 90 degrees to each other.
Versatile CNC machines
Using modern CNC milling and turning machines with the appropriate tools together with technological equipment allows chiseling channels for keys and splines (single or simultaneous), in cylindrical and conical holes (through or blind), with or without chamfering at the base. The key aspect here is the use of feed drives of machine tools: in the case of a milling machine in the Z axis, and in a lathe – in the X axis.
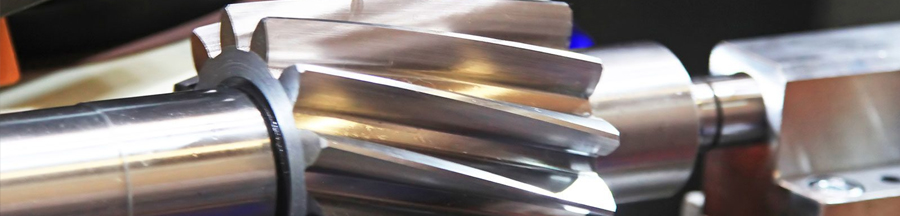
In the past, in extreme cases, chiselling was performed on a lathe with a blocked main drive spindle, and the operator independently carried out the feed movement and idle (return) of the tailstock with the chiselling knife. Modern equipment allows for the machining of shaped holes (e.g. square or hexagonal), as well as with spiral teeth. The machining of shaped holes resembles the broaching process – with the difference that during broaching, the tool performs full processing in one pass, while chiselling requires multiple repetitions of the cycle.
The increasingly popular CNC machine tools facilitate chiseling processes and expand technological possibilities. In practice, techniques commonly considered niche are still used, but more and more often these more traditional manufacturing techniques are being adapted to enable their implementation on numerically controlled machines. The future of such solutions seems interesting in the context of the developed STEP-NC standard used, among others, for programming CNC machine tools.
The article was based on materials from, among others, Eurometal LTD.
Date of publication: 20.10.2022